参观考察一家工厂,如何判断车间的生产管理水平?
作者:鼎捷数智 | 发布时间:2023-06-09 10:14:00
精益生产是制造业提升效率和竞争力的重要思想和方法实践,众多的企业都想要通过精益生产管理提升企业竞争力。
-企业精益管理之“看听问理”-
“看”直观地获得对工厂整体效率的印象
一看员工的工作节奏和表情,员工的工作节奏代表时间分析和现场管理的水平,员工的表情如果比较轻松代表他的工作很顺畅,较少被异常打断。
二看员工是否频繁走动,表示车间异常以及人员的利用率。如果员工频繁离开岗位,现场走动的人较多,那么可能说明流程设计上有问题,管理水平较差。
三看产品是否流动,过程是否有等待,有没有很好的流动起来。工序之间若存在等待说明产线设计平衡率不好,制程不稳定。
四看在制品库存是否可控,各工序之间的在制品数量和原材料库存数量是通过设计计算出来的,是可控制的,最好是有物理限制,不可控则是由工人经验或者流过来多少做多少。
五看设备开动率,表示工厂产能利用情况和订单量状况。
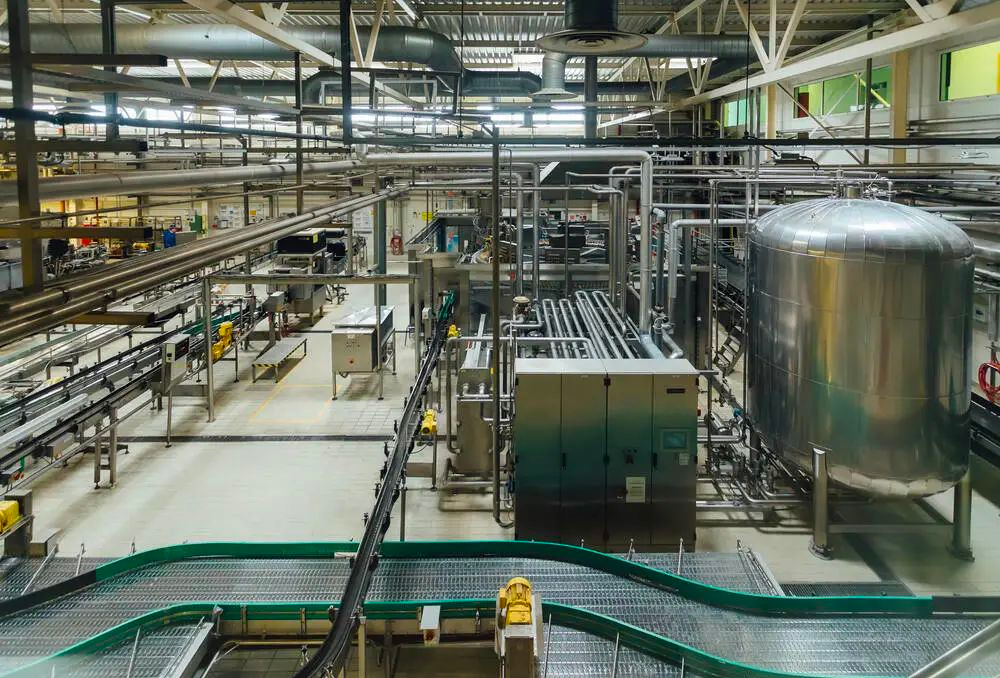
一听车间是否有奇怪的异响,有时在工厂突然听到叮叮当当的敲击声,一般不是产品返修,就是工具工艺有问题。如果噪音很大(如钣金冲床),也需要关注员工安全职业健康防护。
三听有没有员工呼喊声,常常发生的情况:“叫料基本用喊,管人基本用吼。”“叫支援部门半天不来,来了就像吵架。”这都是很典型的传统生产现场现象。
“问”获得企业参与者对企业现状的评价和反馈
一问现场工人,问工人们几个问题,获取我们所关注的信息。
①你对你现在的工作满意么?(看员工满意度)
②你经常向你的主管提建议么?你提出的建议会获得主管的反馈么?(看上下级沟通是否顺畅,员工是否有渠道和意愿参与公司改进)
③你觉得你这个工序活儿难干么?有什么需要改进的地方?(看作业标准化程度)
④你觉得这活儿干着累不累?哪里特别累?(看产线设计的人机工程学合理性)
二问产线班组长,通过交谈了解班组长每天都处理些什么事情,哪些事情占用每天的工作时间最多,哪些事情最为棘手。
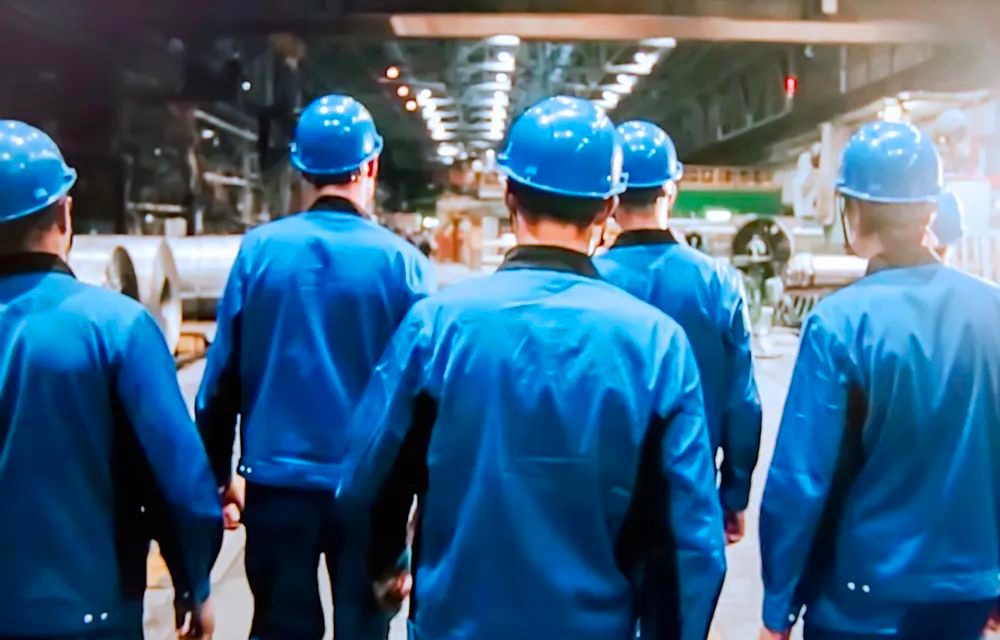
“理”对企业的四个流和管理指标进行梳理
一理,梳理物流。关注工艺流程,生产布局。从材料进厂到成品出厂,沿着工艺流程在各个车间走一遍,绘制整个物流的完整地图。
看工艺设计,工装夹具,设备状况,线体大布局和工位的小布局,了解整体工艺水平。
初步测量产线设计节拍,了解产能瓶颈,在制品堆积点,了解信息传递方法,关键质量风险点,生产计划点,物料供应流,成品及垃圾撤退路线等。
上一页:5000家企业参与!《民营企业数字化转型调研报告》重磅发布
相关新闻
-
喜讯丨鼎捷数智荣获“2022(行业)引领品牌”
前不久,由品牌创新发展大会组委会主办,中国产业经济信息网、搜狐、艾瑞网、Techweb、砍柴网、至顶网等媒体平台联合支持的“2022(第三届)品牌创新发展大会”于北京成功举办。